TPEE Dryer & VOC Cleaner
Application Sample
Raw Material | TPE Pellets by SK Chemical | ![]() ![]() |
Using Machine | LDHW-1200*1000 | ![]() |
Initial moisture | 1370ppm
Tested by German Sartorius Moisture test instrument |
![]() |
Drying Temperature set | 120℃
(material actual temperature during the drying processing) |
|
Drying time set | 20mins | |
Final moisture | 30ppm
Tested by German Sartorius Moisture test instrument |
![]() |
Final product | Dried TPE no clumping, no pellets sticking | ![]() |
How to Work
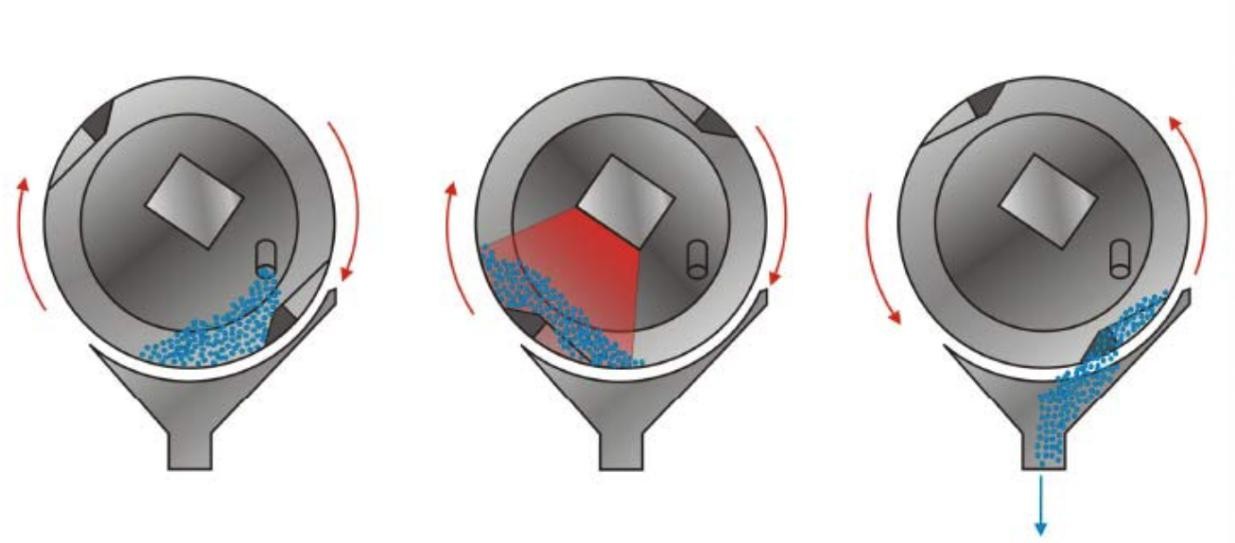
>>At first step, the only target is to heat up the material to a preset temperature.
Adopt relatively slow speed of drum rotating, the Infrared lamps power of the dryer will be at a higher level, then the PETG pellets will have a fast heating till the temperature rises to the preset temperature.
>>Drying step
Once the material gets to the temperature, the speed of the drum will be increased to a much higher rotating speed to avoid the clumping of the material. At the same time, the infrared lamps power will be increased again to finish the drying. Then the drum rotating speed will be slowed down again. Normally the drying process will be finished after 15-20mins. (The exact time depends on the property of material)
>>After finishing the drying processing, the IR Drum will automatically discharge the material to vacuum devolatilization system for VOC Removing
>>Devolatilization system for VOC Removing
The infrared devolatilization system mainly continuously heats the material through the infrared radiation with specific wavelength, while the material is heated up to a preset temperature, the dried material will be fed to Vacuum devolatilization system for repeated vacuumization devolatilization, finally the volatiles which are released by heated material are discharged by Vacuum system. And the Volatile matter content can be <10ppm
Our Advantage
1 | Low energy consumption | Significantly lower energy consumption compared to conventional processes, through the direct introduction of infrared energy to the product |
2 | Minutes instead of hours | The product remains for only a few minutes in the drying process and is then available for further production steps.
|
3 | Instantly | The production run can start immediately upon startup. A warm-up phase of the machine is not required.
|
4 | Gently | The material is heated gently from the inside to the outside and not loaded from the outside for hours with heat, and thereby possibly damaged.
|
5 | In one step | Crystallization and drying in one step |
6 | Increased throughput | Increase of plant throughput by means of reduced load on extruder |
7 | No clumping, no sticking | The rotation of the drum ensures constant movement of the material.
The spiral coils and mixing elements designed for your product ensure an optimal mix of material and avoids clumping. The product is evenly heated |
8 | Siemens PLC control | Control.The process data, such as material and exhaust air temperature or fill levels are continuously monitored by means of sensors and pyrometers. Deviations trigger automatic adjustment.
Reproducibility.Recipes and process parameters can be stored in the controlling system to ensure optimal and reproducible results. Remote maintenance.Online service via modem. |
Machine Photos
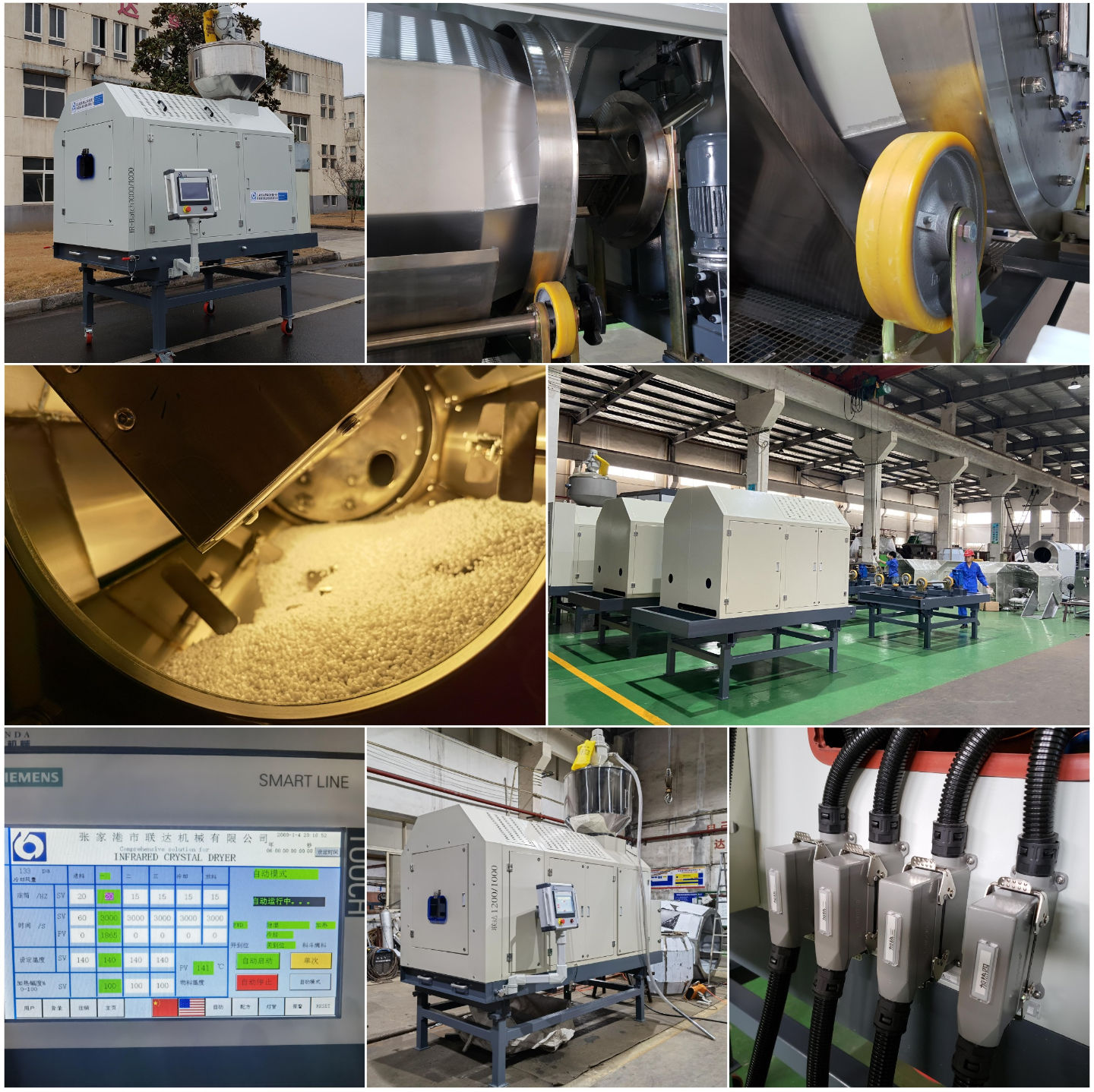
Machine Application
Drying | Drying of plastic granulates ( PET,TPE, PETG, APET, RPET, PBT, ABS/PC, HDPE, LCP, PC,PP , PVB,WPC,TPU etc) as well as other free-flowing bulk materials |
Crystallization | PET (Bottle flakesm granulates, sheet scrap), PET Masterbatch, CO-PET, PBT,PEEK, PLA, PPS etc |
Diverse | Thermal processed for removal of rest oligomeren and volatile components |
Material Free Testing
Our factory has build Test Center. In our Test center, we can perform continuous or discontinuous experiments for customer’s sample material. Our equipment is furnished with comprehensive automation and measurement technology.
• We can demonstrate --- Conveying/Loading, Drying& Crystallization, Discharging.
• Drying and crystallization of material to determine residual moisture, residence time, energy input and material properties.
• We can also demonstrate performance by subcontracting for smaller batches.
• In accordance with your material and production requirements, we can map out a plan with you.
Experienced engineer will make the test. Your employees are cordially invited to participate in our joint trails. Thus you have both the possibility to contribute actively and the opportunity to actually see our products in operation.
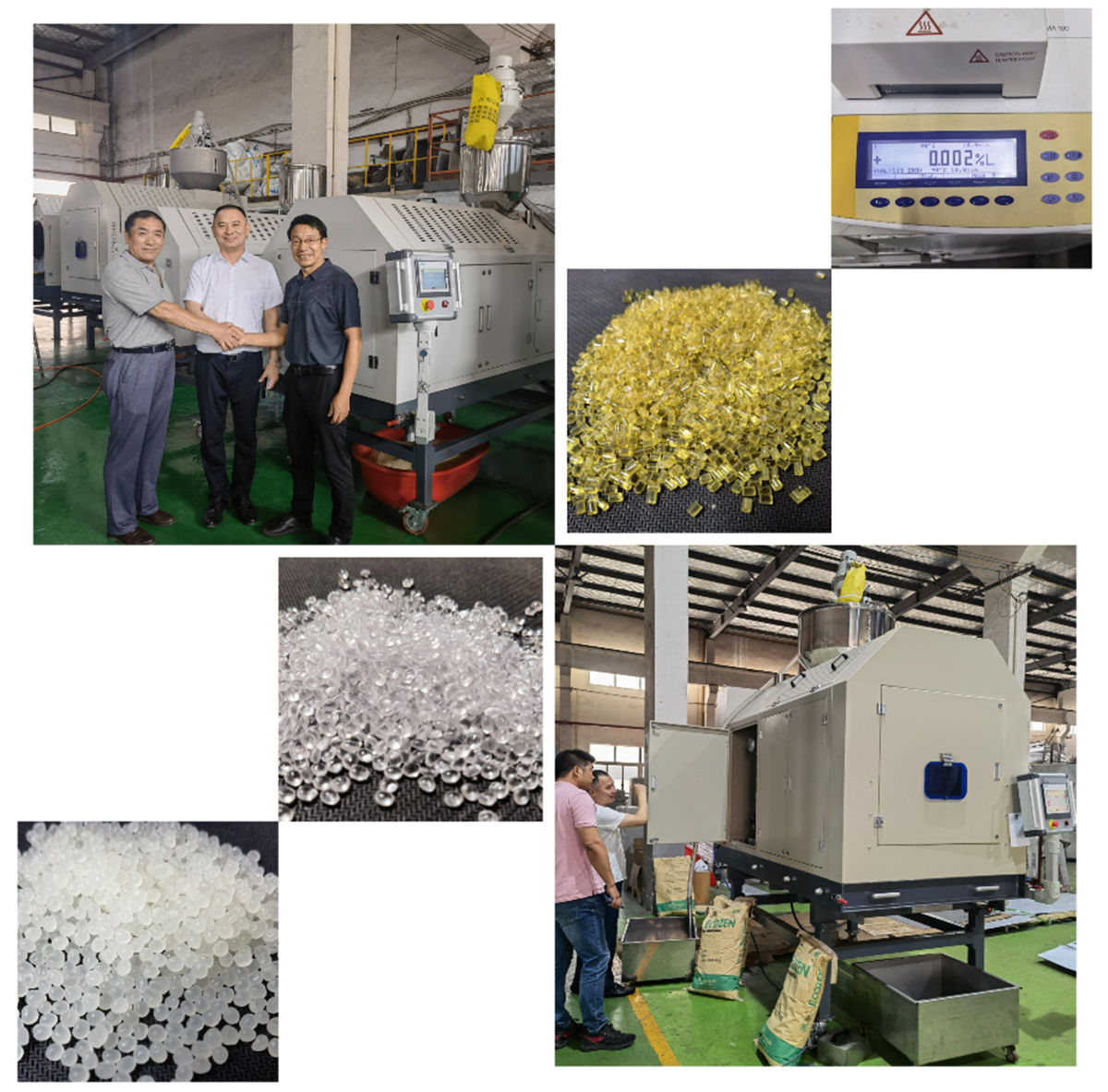
Machine Installation
>> Supply Experienced engineer to your factory to help installation and material test running
>> Adopt aviation plug, no need to connect the electrical wire while the customer get the machine in his factory. To simplify the installation step
>> Supply the operation video for installation and running guide
>>Support on line service
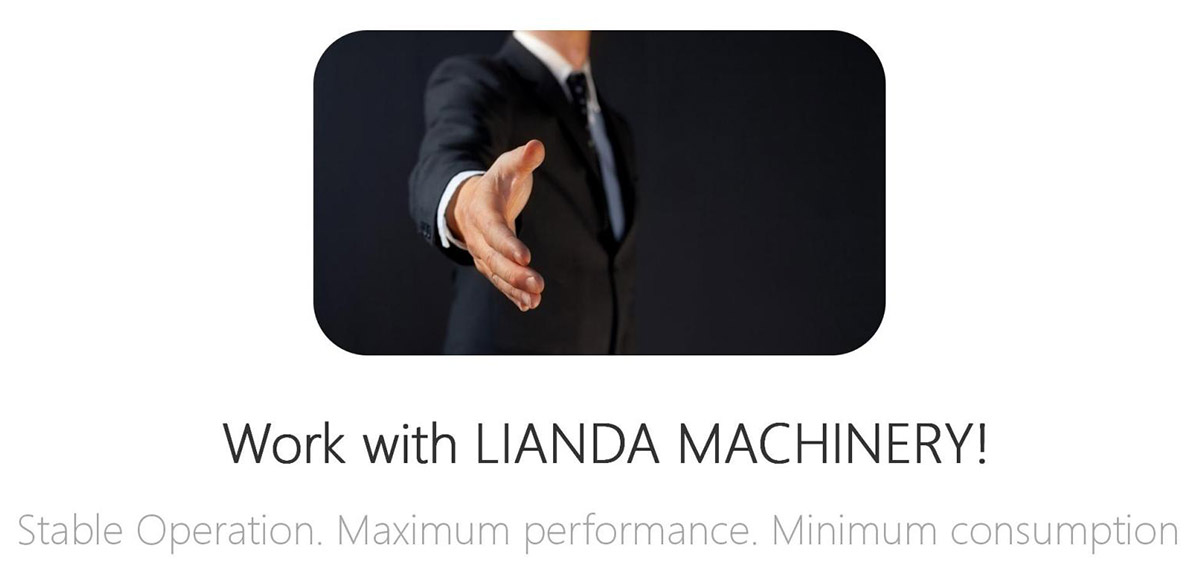