PLA Crystallizer dryer
Application Sample
Raw Material | PLA
Manufactured by Xinjiang Lanshan Tunhe |
![]() |
Using Machine | LDHW-600*1000 | ![]() |
Initial moisture | 9730ppm
(By adding water to PLA Raw material to check how efficient the dryer can make ) Tested by German Sartorius Moisture test instrument |
![]() |
Drying Temperature set | 200℃ | |
Drying time set | 20mins | |
Final moisture | 20ppm
Tested by German Sartorius Moisture test instrument |
![]() |
Final product | Dried PET Resin no clumping, no pellets sticking | ![]() |
How to Work
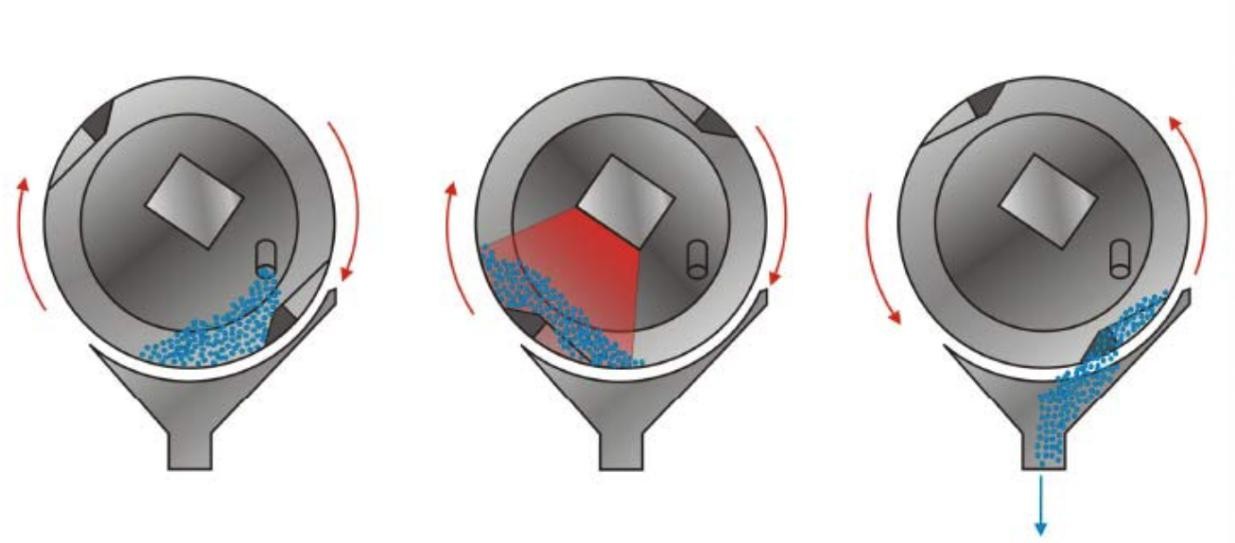
>>At first step, the only target is to heat up the material to a preset temperature.
Adopt relatively slow speed of drum rotating, the Infrared lamps power of the dryer will be at a higher level, then the PET pellets will have a fast heating till the temperature rises to the preset temperature.
>>Drying step
Once the material gets to the temperature, the speed of the drum will be increased to a much higher rotating speed to avoid the clumping of the material. At the same time, the infrared lamps power will be increased again to finish the drying. Then the drum rotating speed will be slowed down again. Normally the drying process will be finished after 15-20mins. (The exact time depends on the property of material)
>>After finishing the drying processing, the IR Drum will automatically discharge the material and refill the drum for the next cycle.
The automatic refilling as well as all relevant parameters for the different temperature ramps is fully integrated in the state-of-the-art Touch Screen control. Once parameters and temperature profiles are found for a specific material, theses settings can be saved as recipes in the control system.
Our Advantage
1 | Low energy consumption | Significantly lower energy consumption compared to conventional processes, through the direct introduction of infrared energy to the product
Save about 40% energy consumption compared with conventional crystallizer and dryer |
2 | Minutes instead of hours | The product remains for only a few minutes in the drying process and is then available for further production steps.
|
3 | Easy to clean | The drum can be opened completely,no hidden spots and can be cleaned easily with a vacuum cleaner |
4 | No clumping | Rotary drying system, its rotating speed can be increased as high as possible to get an excellent mixing of pellets. It is good in agitation, the material will not be clumped |
5 | Temperature set independently | The drum is divided into three heating zones which equipped with infrared PID temperature sensors can be set drying or crystallized temperature independently.
|
6 | Siemens PLC Touch screen control | Infrared rotary dryer is designed with sophisticated temperature measurement. The material and exhaust air temperature are continuously monitored by sensors. If there is any deviations,PLC system will adjust automatically |
Recipes and process parameters can be stored in the controlling system to ensure optimal and reproducible results | ||
Easy to operate |
Machine Photos
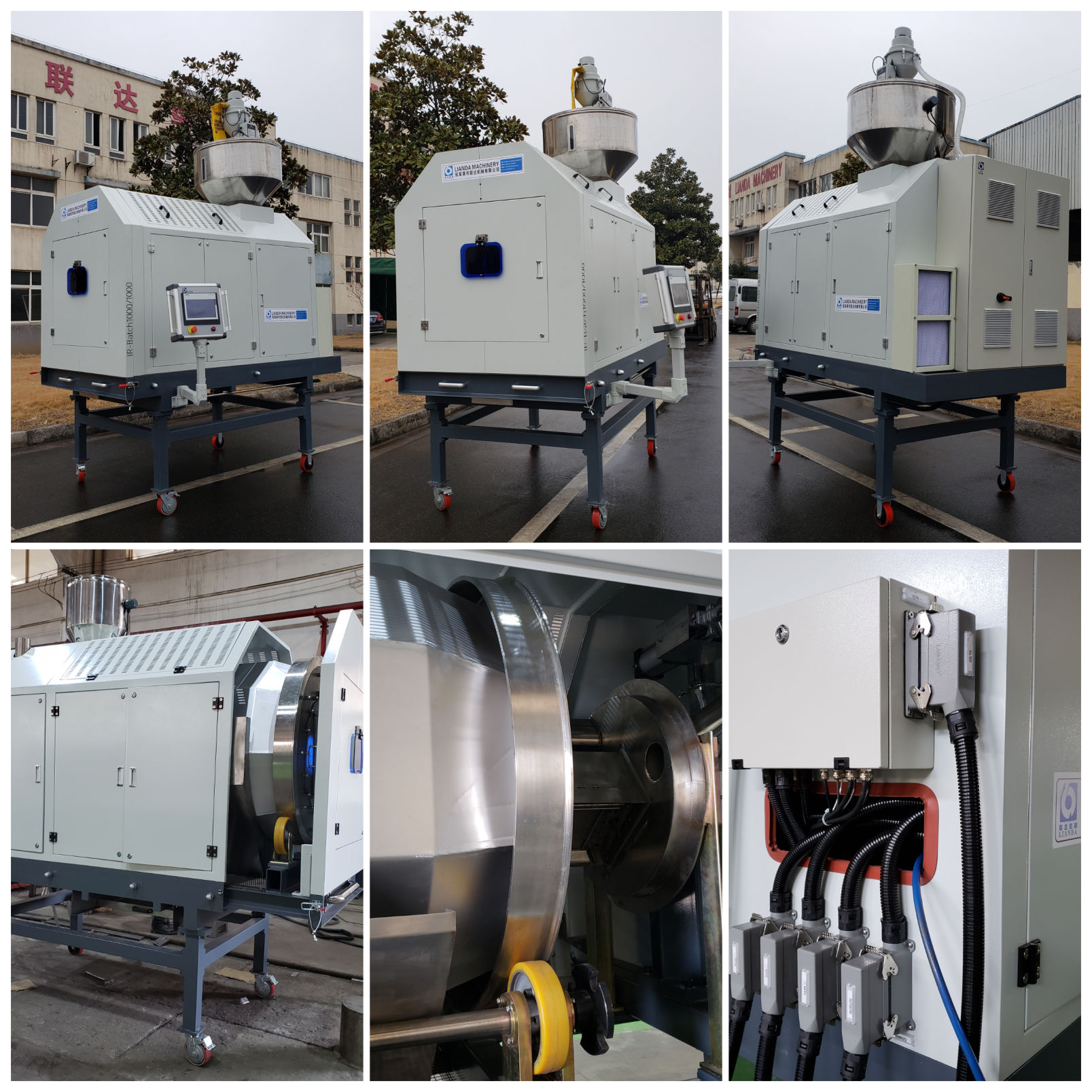
Machine Application
Heating. | Heating granules and regrind material prior to further processing (e.g. PVC, PE, PP,…) to improve
throughput in the extrusion process.
|
Crystallization | Crystallization of PET (Bottle flakes, granules, flakes), PET masterbatch, co-PET, PBT, PEEK, PLA, PPS, etc. |
Drying | Drying of plastic granules, and ground material (e.g. PET, PBT, ABS/PC, HDPE, LCP, PC, PP, PVB, WPC, TPE, TPU) as well as other free-flowing bulk materials. |
High-input moisture | Drying processes with high input moisture >1% |
Diverse | Heating processes for the removal of rest oligomers and volatile components. |
Material Free Testing
Experienced engineer will make the test. Your employees are cordially invited to participate in our joint trails. Thus you have both the possibility to contribute actively and the opportunity to actually see our products in operation.
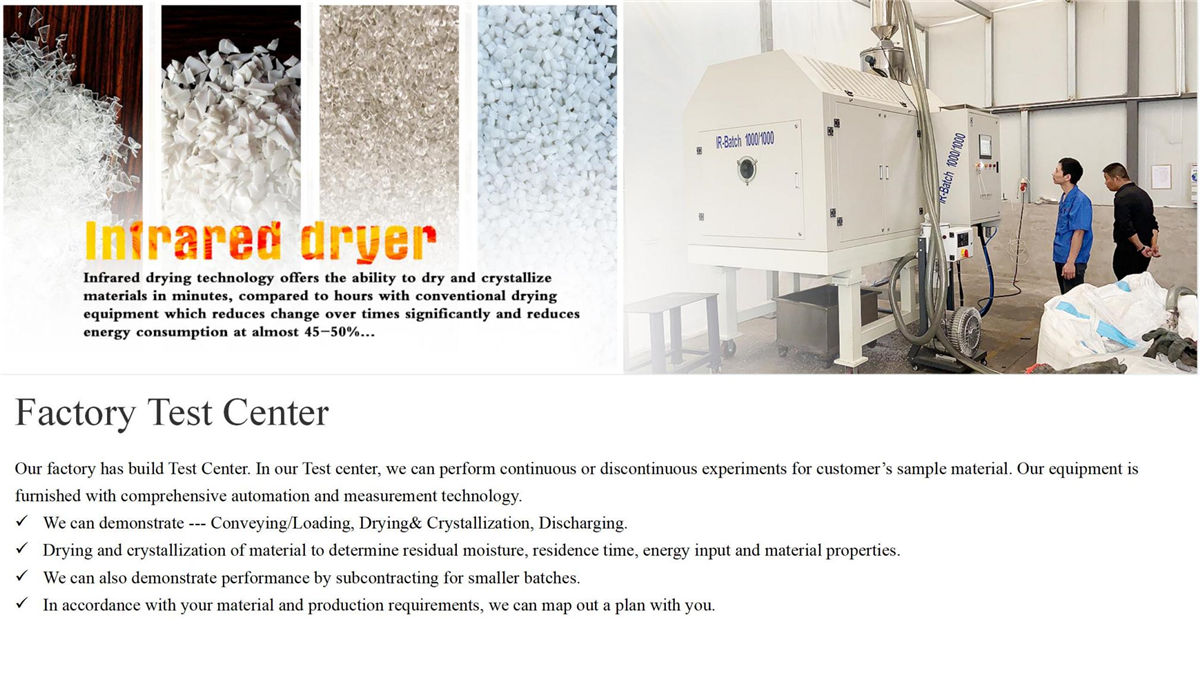
Machine Installation
>> Supply Experienced engineer to your factory to help installation and material test running
>> Adopt aviation plug, no need to connect the electrical wire while the customer get the machine in his factory. To simplify the installation step
>> Supply the operation video for installation and running guide
>>Support on line service
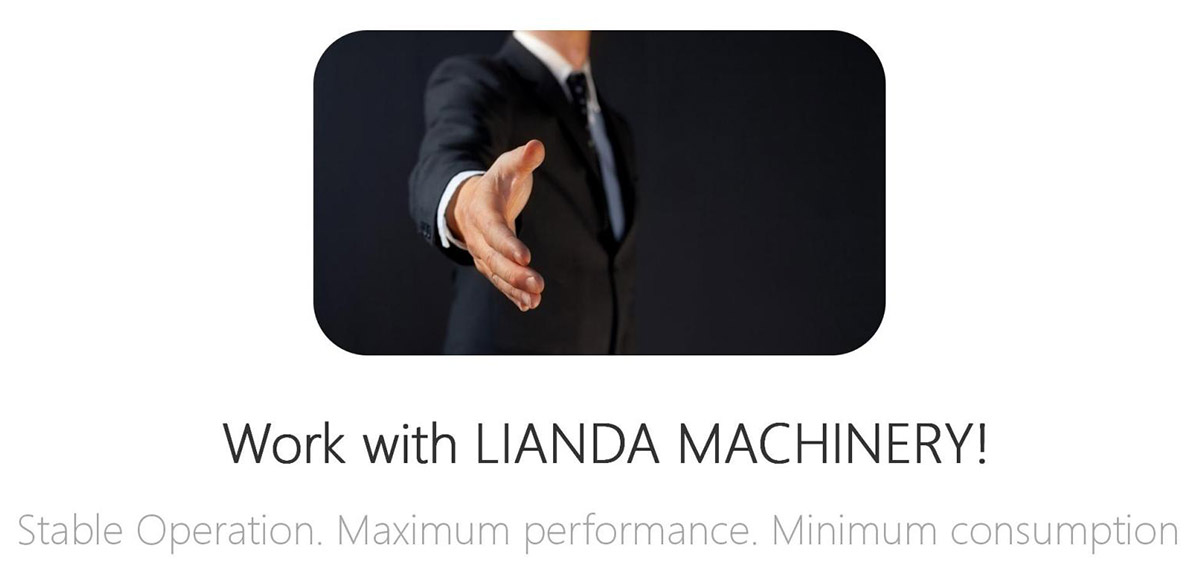